Listen to this text |
Now a completely modular and easy-to-program robotics expertise lets engineers and different plant personnel shortly choose and join kinematic modules to create industrial robotic arms.
Sponsored content material ⚙️ Traditional six-axis serial robotics and selective compliance meeting robotic arms (SCARAs) have prebuilt buildings and rigidly outlined motions and levels of freedom (DOFs). In distinction, now a wholly new sequence of field-assemblable robots is each programmatically and bodily configurable (and reconfigurable) by engineers and plant workers alike. Called Automation Technology for Robotics or ATRO, every accomplished meeting consists of a base module and a novel mixture of different modules (every acknowledged as separate EtherCAT gadgets by controls) to make functioning robotic tables, arms, or delta assemblies.
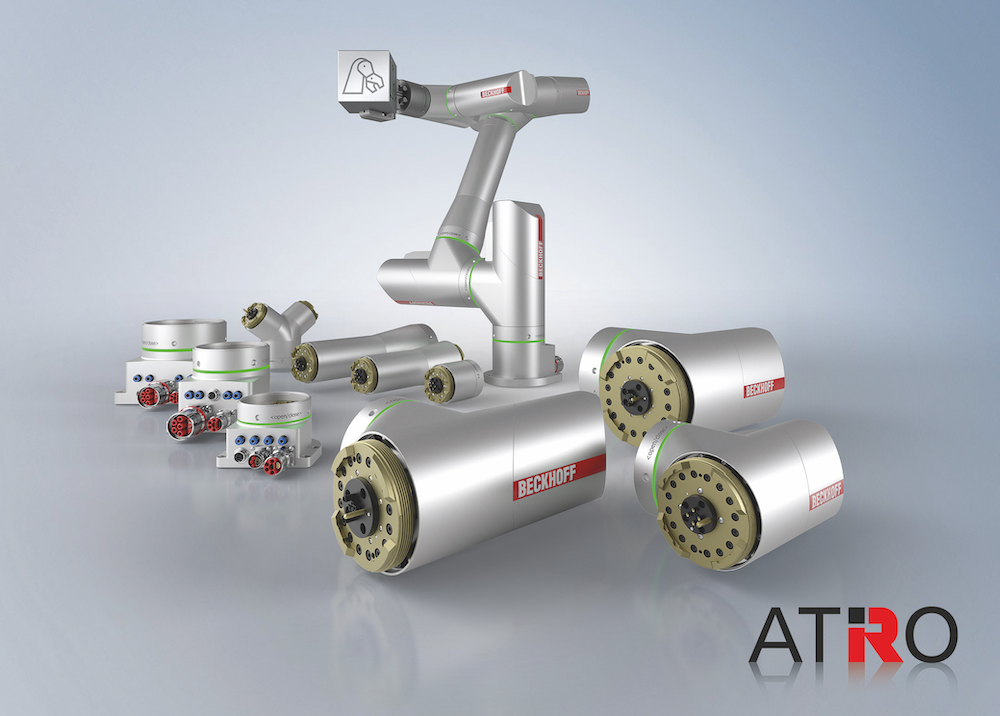
The Automation Technology for Robotics (ATRO) from Beckhoff Automation is a versatile and absolutely built-in multi-axis system that helps speedy robotic meeting and programming.
In truth, ATRO enhances different applied sciences within the movement provider’s New Automation Technology product vary — together with PC-based management, industrial PCs, automation controllers, operator interfaces, I/O, servo drives, and motors.
More particularly, ATRO kinematics are constructed of modules from 4 classes.
ATRO base modules (the primary upon which different modules are stacked) embrace a ruggedized base with mounting flanges, energy and networking connectivity ports, and an output media feed that begins the interior run of media by means of the meeting’s inside to permit limitless joint rotations. (More on this shortly.)
Active motorized modules are open-ended arm sections containing a planetary gearmotor, brake, servodrive, and management electronics in a ruggedized cylindrical housing. Ends are threaded and studded with mechanical locking Hirth joints to shortly safe to different modules within the sequence.
These subsystems are available quite a lot of diameters, lengths, and shapes; each straight I-shape and angled L-shape motorized modules are available 5 energy sizes. Because every lively module types an entire drive system for one robotic axis, the one exterior elements wanted are an influence provide and controller. It’s a construction that considerably reduces the quantity of control-cabinet actual property consumed by {hardware} to command the robotic’s DOFs.
After programming, ATRO robotics use EtherCAT for direct integration into PC-based controls for mechanically optimized workcells. In truth, one industrial PC can command a number of ATRO robots. Besides simplifying set up, that may additionally trim price.
Connection or linkage modules are available I, L, and Y shapes and permit additional customization of the robotic morphology. Featuring the identical ruggedized housings and mechanical end-connection geometries because the ATRO system’s motorized modules, these function the movable joints of ATRO assemblies.
Finally, user-specified system modules combine application-specific gripping or different end-effector features. With these core module choices, an enormous array of robotics is feasible, together with:
• Single-axis rotary indexing tables and two-axis trackers
• Three-axis delta robots (with supporting {hardware}) and four-axis pick-and-place robots
• Five-axis palletizing arms
• Six-axis serial arms
• Seven-axis robotics able to specialty articulation for machine tending and related duties necessitating extension into hard-to-reach areas inside equipment.
In some circumstances, the automation answer’s mechanics and half depend might be lowered. ATRO’s extraordinarily versatile construction lets it fulfill quite a lot of purposes — even these involving payloads to 10 kg and reaches to 1.3 m.
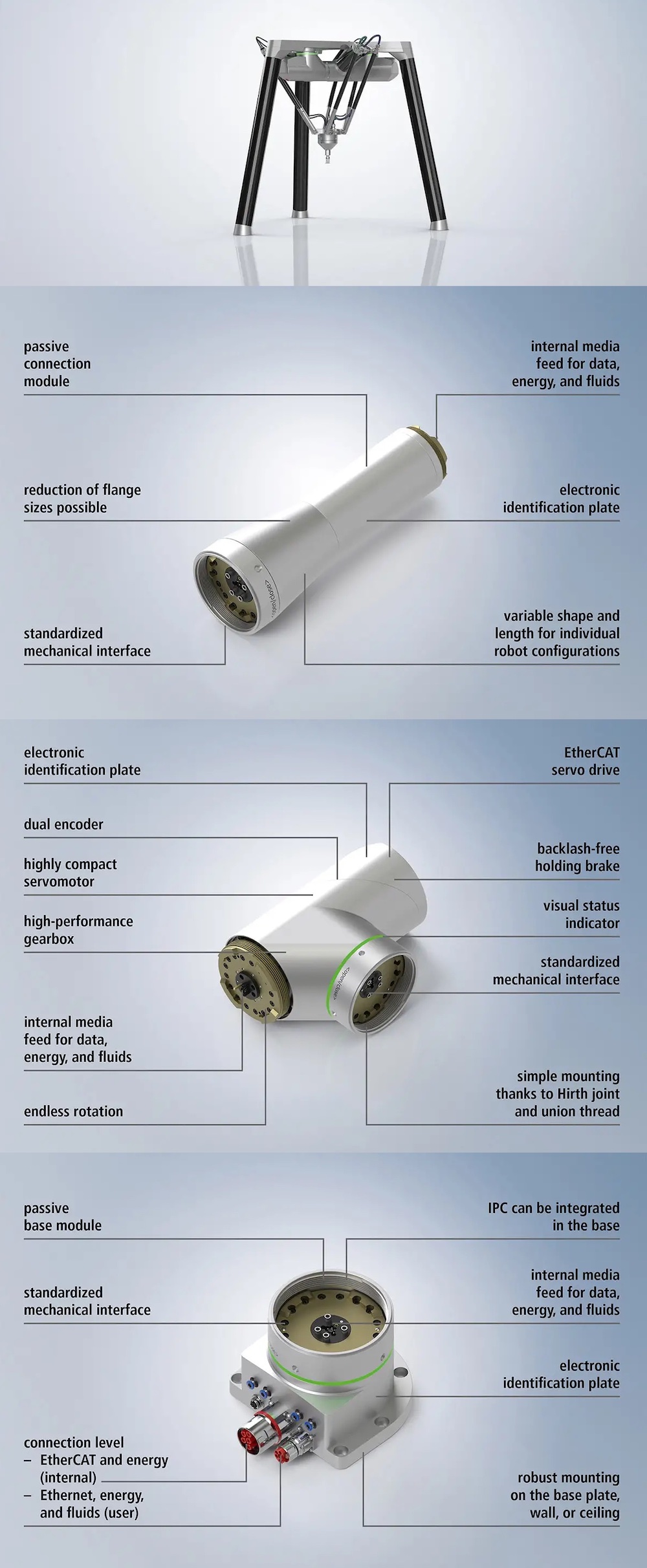
ATRO methods from Beckhoff adapt to duties needing multi-axis movement. They’re additionally freely scalable, customizable, and expandable.
Programming and controlling ATRO robots
ATRO options EtherCAT connectivity that enhances the best way during which the robotic modules are commissioned and programmed by way of TwinCAT software program. The latter contains a huge mannequin library to help customary in addition to customized industrial kinematics for simpler integration of robotic handlers into machine workcells. In distinction, conventional off-the-shelf SCARA and glued serial robots are hardly ever an ideal match for pre-existing or finalized workcell parts … thus complicating the setup of real-world purposes.
The ATRO interface inside TwinCAT helps 3D simulation of single robots to let finish customers construct robots themselves utilizing the bottom, lively, and linkage modules simply described. From there, digital workpieces, trays, tables, baskets, machine entry home windows, imported machine CAD recordsdata, and obstacles (equivalent to pillars, partitions, and workcell fencing) within the TwinCAT GUI might be modeled to let the person outline how the robotic ought to work together with or keep away from them.
Pick, flip, place, and myriad different strikes might be set within the desired sequence after which exported.
Once the controller receives the exported file, it builds the complete PLC code. Then customers merely log into the controller by way of the GUI and click on an allow button to run the robotic by means of its motions. Coordination with superior conveying methods and even levitating motor installations is feasible, as are expansive configurations with as many as 16 ATRO robots.
Structures are merely scanned by the management software program, and the TwinCAT robotic features mechanically create the corresponding management utility — together with a digital twin. (Where wanted, the digital twin inside TwinCAT can outline stresses on ATRO’s mechanical elements.) In-the-field educating of ATRO methods is equally simple; customers merely seize the robotic, transfer its related modules by means of desired positions, and set the trail and factors by way of a related HMI.
To be clear, customers with totally different skillsets can select from three programming choices — fundamental routines (for guide robotic educating), reasonably subtle routines (for customers who really feel comfy constructing, importing, and defining machine parts), and superior routines for TwinCAT consultants with proficiency in 3D simulation, coding operations, and line-by-line tweaking of mechanically generated programming (as IEC 61131-3 structured textual content, ladder logic, or function-block diagrams — FBDs).
Physical system connections and communications
ATRO’s tight TwinCAT integration permits management of a number of robots by way of one controller. Even machine-vision picture processing, machine studying, practical security, and direct cloud integration (to help enterprise-level evaluation and predictive upkeep routines) are doable. Synchronization of ATRO methods with XTS and XPlanar adaptive product dealing with methods inside this widespread setting minimizes communication delays. As talked about, ATRO methods may also endlessly rotate at every joint. That’s on account of:
• The gearmotor design in lively modules
• Multi-turn servo-axis monitoring of place
• Routing of energy, communications, and different fluid media by means of the middle of every robotic module by way of rotary unions and Hirth joints.
The latter is especially considerably distinctive — particularly as connections embrace 4 for compressed air, vacuums, water, and different fluids; EtherCAT and Gbit Ethernet; and 48-V in addition to high-voltage AC energy. All these connections render the ATRO able to accepting varied distributors’ finish effectors and grippers (whether or not electromagnetic or pneumatic) which by definition are exceptionally job particular.
Where may limitless joint rotation show helpful? Well, this provides ATRO methods most reachability in addition to the flexibility to take particularly quick (learn: quick) paths to achieve given positions in 3D house. What’s extra, it eliminates the bulkiness of cables run alongside the robotic’s exterior in addition to interfering torques so widespread in robots and collaborative robots (cobots).
The use of EtherCAT-standard LED communications (within the type of illuminated bands on each ATRO module) offers native diagnostics info. A module glowing blue signifies the ATRO is in educating mode. Green signifies the module has a dependable connection and is able to function. Yellow signifies that an operation is being processed; pink signifies the presence of a difficulty.
What prompted ATRO improvement — and rising purposes
ATRO satisfies a necessity for easy-to-assemble customized machine-tending choices, particularly these requiring arms able to reaching round obstacles inside giant tools. Its customizable kinematics may also deal with variable payloads and execute notably difficult motions. Consider an utility from the machine-tool business — that of milling. Here, ATRO controls can nimbly interpolate the movement wanted from the top effector to know, orient, and cargo workpieces into the machine … after which nimbly reverse the method as soon as milling is full.
Though ATRO methods aren’t but licensed to be used as cobots, they do embrace 17 totally different drive-based security modes, together with restricted velocity and secure acceleration settings. The first cutting-edge ATRO permutations have taken the type of so-called octo-robots for superior meeting and materials dealing with purposes.
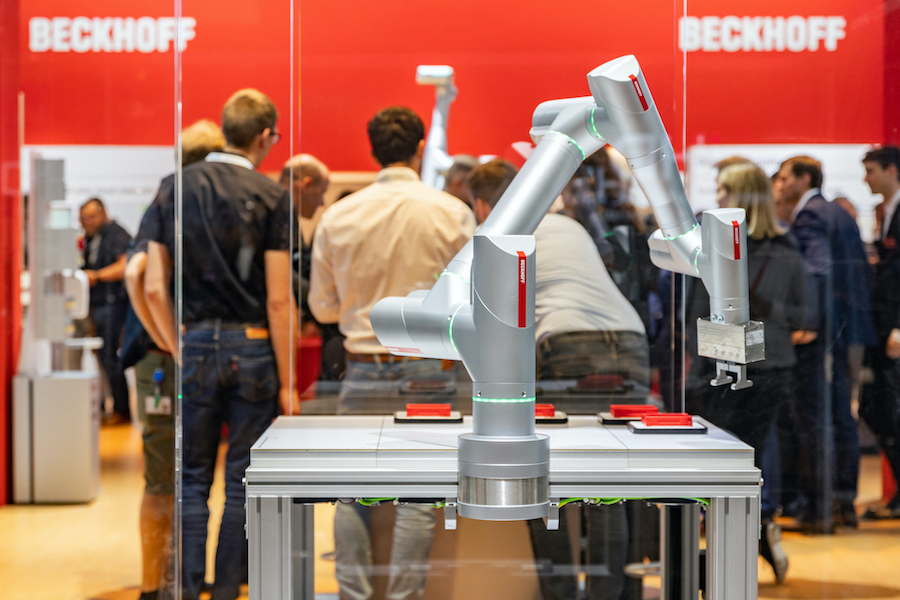
Beckhoff ATRO robotics are appropriate to be used in intralogistics, materials dealing with, fabrication, medical meeting, and packaging purposes.
Beckhoff Automation | www.beckhoff.com