A brand new kind of fabric can be taught and enhance its capacity to cope with sudden forces because of a singular lattice construction with connections of variable stiffness, as described in a brand new paper by my colleagues and me.
The new materials is a sort of architected materials, which will get its properties primarily from the geometry and particular traits of its design relatively than what it’s made out of. Take hook-and-loop material closures like Velcro, for instance. It doesn’t matter whether or not it’s comprised of cotton, plastic or another substance. As lengthy as one aspect is a material with stiff hooks and the opposite aspect has fluffy loops, the fabric may have the sticky properties of Velcro.
My colleagues and I based mostly our new materials’s structure on that of a synthetic neural community—layers of interconnected nodes that may be taught to do duties by altering how a lot significance, or weight, they place on every connection. We hypothesized {that a} mechanical lattice with bodily nodes could possibly be skilled to tackle sure mechanical properties by adjusting every connection’s rigidity.
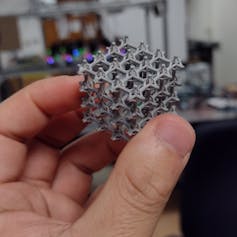
To discover out if a mechanical lattice would be capable of undertake and keep new properties—like taking over a brand new form or altering directional energy—we began off by constructing a pc mannequin. We then chosen a desired form for the fabric in addition to enter forces and had a pc algorithm tune the tensions of the connections in order that the enter forces would produce the specified form. We did this coaching on 200 totally different lattice constructions and located {that a} triangular lattice was greatest at reaching all the shapes we examined.
Once the numerous connections are tuned to attain a set of duties, the fabric will proceed to react within the desired approach. The coaching is—in a way—remembered within the construction of the fabric itself.
We then constructed a bodily prototype lattice with adjustable electromechanical springs organized in a triangular lattice. The prototype is product of 6-inch connections and is about 2 ft lengthy by 1½ ft vast. And it labored. When the lattice and algorithm labored collectively, the fabric was capable of be taught and alter form specifically methods when subjected to totally different forces. We name this new materials a mechanical neural community.
Why It Matters
Besides some residing tissues, only a few supplies can be taught to be higher at coping with unanticipated hundreds. Imagine a airplane wing that immediately catches a gust of wind and is pressured in an unanticipated route. The wing can’t change its design to be stronger in that route.
The prototype lattice materials we designed can adapt to altering or unknown circumstances. In a wing, for instance, these modifications could possibly be the buildup of inner harm, modifications in how the wing is hooked up to a craft, or fluctuating exterior hundreds. Every time a wing made out of a mechanical neural community skilled one in all these eventualities, it may strengthen and soften its connections to keep up desired attributes like directional energy. Over time, by way of successive changes made by the algorithm, the wing adopts and maintains new properties, including every habits to the remaining as a form of muscle reminiscence.
This kind of fabric may have far reaching purposes for the longevity and effectivity of constructed constructions. Not solely may a wing product of a mechanical neural community materials be stronger, it is also skilled to morph into shapes that maximize gasoline effectivity in response to altering circumstances round it.
What’s Still Not Known
So far, our workforce has labored solely with 2D lattices. But utilizing laptop modeling, we predict that 3D lattices would have a a lot bigger capability for studying and adaptation. This improve is because of the truth that a 3D construction may have tens of instances extra connections, or springs, that don’t intersect with each other. However, the mechanisms we utilized in our first mannequin are far too advanced to assist in a big 3D construction.
What’s Next
The materials my colleagues and I created is a proof of idea and exhibits the potential of mechanical neural networks. But to deliver this concept into the actual world would require determining how you can make the person items smaller and with exact properties of flex and rigidity.
We hope new analysis within the manufacturing of supplies on the micron scale, in addition to work on new supplies with adjustable stiffness, will result in advances that make highly effective sensible mechanical neural networks with micron-scale components and dense 3D connections a ubiquitous actuality within the close to future.
This article is republished from The Conversation below a Creative Commons license. Read the authentic article.
Image Credit: Flexible Research Group at UCLA