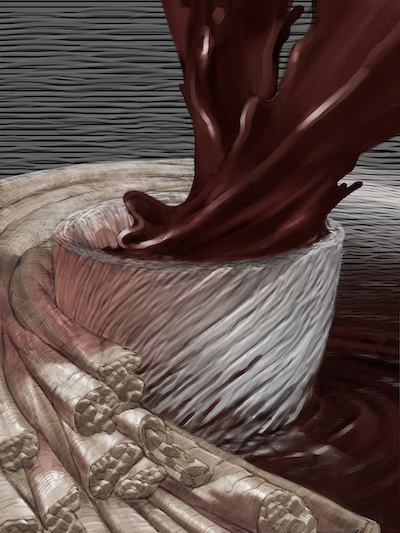
This illustration reveals a 3D printed coronary heart ventricle engineered with fiber-infused ink. Credit: Harvard SEAS
By Kat J. McAlpine / SEAS Communications
Over the final decade, advances in 3D printing have unlocked new potentialities for bioengineers to construct coronary heart tissues and constructions. Their objectives embody creating higher in vitro platforms for locating new therapeutics for coronary heart illness, the main reason behind loss of life within the United States, answerable for about one in each 5 deaths nationally, and utilizing 3D-printed cardiac tissues to guage which therapies would possibly work finest in particular person sufferers. A extra distant intention is to manufacture implantable tissues that may heal or exchange defective or diseased constructions inside a affected person’s coronary heart.
In a paper revealed in Nature Materials, researchers from Harvard John A. Paulson School of Engineering and Applied Sciences (SEAS) and the Wyss Institute for Biologically Inspired Engineering at Harvard University report the event of a brand new hydrogel ink infused with gelatin fibers that permits 3D printing of a practical coronary heart ventricle that mimics beating like a human coronary heart. They found the fiber-infused gel (FIG) ink permits coronary heart muscle cells printed within the form of a ventricle to align and beat in coordination like a human coronary heart chamber.
“People have been trying to replicate organ structures and functions to test drug safety and efficacy as a way of predicting what might happen in the clinical setting,” says Suji Choi, analysis affiliate at SEAS and first writer on the paper. But till now, 3D printing strategies alone haven’t been capable of obtain physiologically-relevant alignment of cardiomyocytes, the cells answerable for transmitting electrical indicators in a coordinated style to contract coronary heart muscle.
“We started this project to address some of the inadequacies in 3D printing of biological tissues.”
– Kevin “Kit” Parker
The innovation lies within the addition of fibers inside a printable ink. “FIG ink is capable of flowing through the printing nozzle but, once the structure is printed, it maintains its 3D shape,” says Choi. “Because of those properties, I found it’s possible to print a ventricle-like structure and other complex 3D shapes without using extra support materials or scaffolds.”
This video reveals the spontaneous beating of a 3D-printed coronary heart muscle. Credit: Harvard SEAS.
To create the FIG ink, Choi leveraged a rotary jet spinning method developed within the lab of Kevin “Kit” Parker, Ph.D. that fabricates microfiber supplies utilizing an method much like the way in which cotton sweet is spun. Postdoctoral researcher and Wyss Lumineer Luke MacQueen, a co-author on the paper, proposed the concept that fibers created by the rotary jet spinning method could possibly be added to an ink and 3D printed. Parker is a Wyss Associate Faculty member and the Tarr Family Professor of Bioengineering and Applied Physics at SEAS.
“When Luke developed this concept, the vision was to broaden the range of spatial scales that could be printed with 3D printers by dropping the bottom out of the lower limits, taking it down to the nanometer scale,” Parker says. “The advantage of producing the fibers with rotary jet spinning rather than electrospinning” – a extra typical technique for producing ultrathin fibers – “is that we can use proteins that would otherwise be degraded by the electrical fields in electrospinning.”
Using the rotary jet to spin gelatin fibers, Choi produced a sheet of fabric with an analogous look to cotton. Next, she used sonification – sound waves – to interrupt that sheet into fibers about 80 to 100 micrometers lengthy and about 5 to 10 micrometers in diameter. Then, she dispersed these fibers right into a hydrogel ink.
“This concept is broadly applicable – we can use our fiber-spinning technique to reliably produce fibers in the lengths and shapes we want.”
– Suji Choi
The most troublesome side was troubleshooting the specified ratio between fibers and hydrogel within the ink to keep up fiber alignment and the general integrity of the 3D-printed construction.
As Choi printed 2D and 3D constructions utilizing FIG ink, the cardiomyocytes lined up in tandem with the route of the fibers contained in the ink. By controlling the printing route, Choi may due to this fact management how the center muscle cells would align.
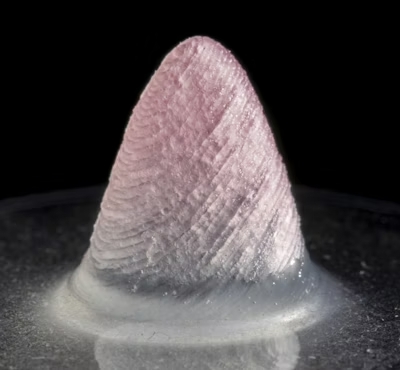
The tissue-engineered 3D ventricle mannequin. Credit: Harvard SEAS
When she utilized electrical stimulation to 3D-printed constructions made with FIG ink, she discovered it triggered a coordinated wave of contractions in alignment with the route of these fibers. In a ventricle-shaped construction, “it was very exciting to see the chamber actually pumping in a similar way to how real heart ventricles pump,” Choi says.
As she experimented with extra printing instructions and ink formulation, she discovered she may generate even stronger contractions inside ventricle-like shapes.
“Compared to the real heart, our ventricle model is simplified and miniaturized,” she says. The crew is now working towards constructing extra life-like coronary heart tissues with thicker muscle partitions that may pump fluid extra strongly. Despite not being as robust as actual coronary heart tissue, the 3D-printed ventricle may pump 5-20 occasions extra fluid quantity than earlier 3D-printed coronary heart chambers.
The crew says the method can be used to construct coronary heart valves, dual-chambered miniature hearts, and extra.
“FIGs are but one tool we have developed for additive manufacturing,” Parker says. “We have other methods in development as we continue our quest to build human tissues for regenerative therapeutics. The goal is not to be tool driven – we are tool agnostic in our search for a better way to build biology.”
Additional authors embody Keel Yong Lee, Sean L. Kim, Huibin Chang, John F. Zimmerman, Qianru Jin, Michael M. Peters, Herdeline Ann M. Ardoña, Xujie Liu, Ann-Caroline Heiler, Rudy Gabardi, Collin Richardson, William T. Pu, and Andreas Bausch.
This work was sponsored by SEAS; the National Science Foundation via the Harvard University Materials Research Science and Engineering Center (DMR-1420570, DMR-2011754); the National Institutes of Health and National Center for Advancing Translational Sciences (UH3HL141798, 225 UG3TR003279); the Harvard University Center for Nanoscale Systems (CNS), a member of the National Nanotechnology Coordinated Infrastructure Network (NNCI) which is supported by the National Science Foundation (ECCS-2025158, S10OD023519); and the American Chemical Society’s Irving S. Sigal Postdoctoral Fellowships.
Wyss Institute
makes use of Nature’s design rules to develop bioinspired supplies and units that may rework medication and create a extra sustainable world.
Wyss Institute
makes use of Nature’s design rules to develop bioinspired supplies and units that may rework medication and create a extra sustainable world.