Listen to this text |
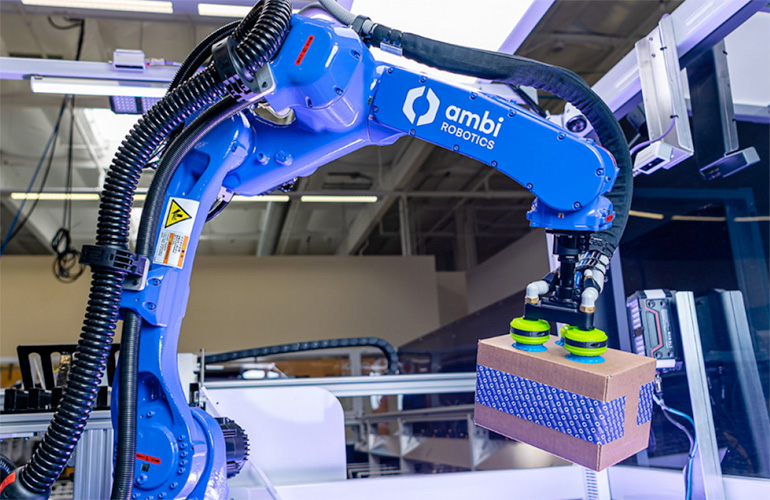
Ambi Robotics warehouse automation answer automates merchandise choosing operations. | Credit: Ambi Robotics
AmbiEntry, a cloud-based enterprise intelligence instrument from Ambi Robotics, helps prospects maximize their Robots-as-a-Service (RaaS) funding. AmbiEntry optimizes operations and maximizes effectivity with superior fleet administration and real-time analytics for world shippers and logistics organizations.
“We built the AmbiAccess platform with a suite of operation-enhancing applications to make our customers’ lives easier,” explains Ambi Robotics co-founder and CTO Jeff Mahler. “This new customer portal goes beyond data visibility, with comprehensive insights and advanced analytics that leverage historical data and trends. Now our customers can better understand the performance of their entire fleet, compare KPIs between facilities and regions, and access real-time analytics from any device.”
As corporations deploy AI-powered robotic sorting programs throughout their networks, the AmbiEntry platform simplifies fleet administration. On-demand entry to data-driven enterprise intelligence helps prospects perceive their operations. Customers might view real-time robotic fleet efficiency, superior analytics reviews, actionable insights, the system’s information library, and 24/7 buyer help in a single spot. Real-time knowledge data productiveness, system utilization, merchandise evaluation, and proactive insights to establish potential points.
“AmbiAccess opens the doors to a more efficient and sustainable supply chain,” says Ambi Robotics VP of Operations Stephen McKinley. “This new platform demonstrates the impact of our AI-powered robotic sorting systems and allows our customers to gain an even greater competitive edge in the market.”
AmbiEntry automates throughput, type plans, exception objects, and operational effectiveness. Customers can evaluate system, facility, and regional developments and metrics. The cloud-based platform lets warehouse managers and operations executives view metrics from anyplace.