The US has a housing scarcity downside. We even have a plastic waste downside. What if we may clear up each these issues concurrently with an sudden two birds/one stone innovation? If you’ve ever longed to stay in a small home made out of 100,000 recycled plastic water bottles, your fortunate day is simply across the nook.
If, like most of us, dwelling in a water-bottle home isn’t in your checklist of life targets, however this nonetheless feels like an intriguing concept, bear with me.
3D printed homes can’t fairly be referred to as “commonplace” but, however they’re rising in recognition and arising in all places from New York to Virginia, California to Texas and in between. If placing down layers of cement wasn’t revolutionary sufficient, an organization referred to as Azure is making good use of the fabric that’s each a boon to our shopper society and the bane of our (and the planet’s) existence: plastic.
Los Angeles-based Azure Printed Homes was based by entrepreneurs Ross Maguire and Gene Eidelman, who imagine they will construct properties 70 p.c quicker, at a price 20 to 30 p.c inexpensive than conventional building strategies—and much more sustainably besides.
Azure’s 3D printed studios and accent dwelling items (ADUs) have been obtainable for preorder since August, and this fall the corporate was chosen by actual property growth firm Re-Inhabit to construct 10 rentable properties in southern California.
“California, like many states, needs to find more innovative ways to speed up the time it takes to build,” stated Re-Inhabit cofounders Rudy and Kim Dvorak in a press launch. “Azure is doing something really special with their approach to the problem. Repurposing materials and 3D printing a complete structure in a fraction of the time is something that is a game changer for us.”
Azure’s course of differs a bit from that of current 3D printed concrete properties. Because concrete is way heavier than plastic, it makes probably the most sense to carry an enormous 3D printer—most of which both transfer across the print space on rails or hold gantry-style from a body—to the house’s location and construct onsite. This provides value and time, although, as a result of the constructing firm wants to maneuver its building gear round and set it up over again at every new residence web site.
Azure is taking a extra centralized strategy. They 3D print the ground, roof, and partitions of their properties of their 10,000-square-foot manufacturing unit in Culver City (exterior LA). By the time a house leaves the manufacturing unit, it’s 99 p.c full; it will get shipped to its web site on a flatbed truck, and all that’s left to do is join the modules to at least one one other and to the muse and utilities.
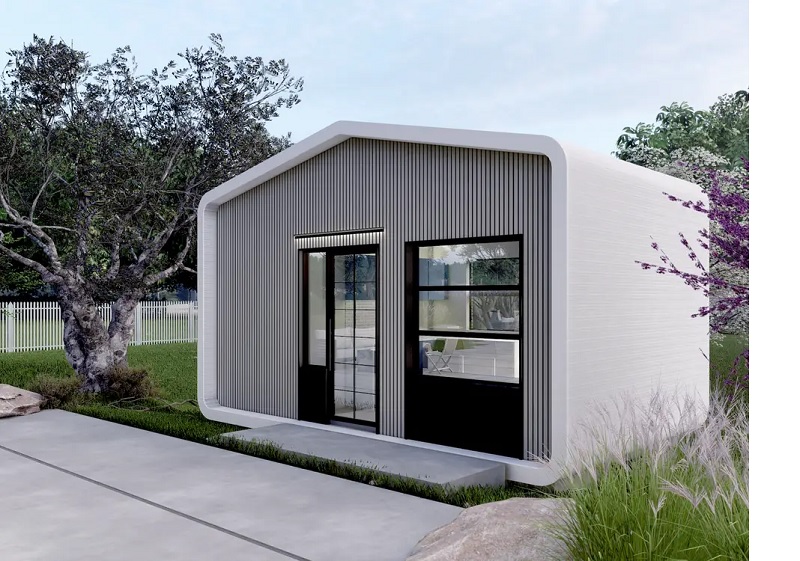
As for the printing portion, it solely takes a day. Over 60 p.c of the printing materials is recycled plastic, which is mixed with different supplies so as to add power and sturdiness. Azure is at present utilizing post-industrial plastic, however hopes to make use of post-consumer plastic within the close to future. Either means, there’ll be plastic to spare; “Our supply chain should never be short in our lifetime,” Maguire advised Business Insider. Not within the subsequent lifetime, both.
On prime of placing recycled plastic to good use, Azure is making the properties themselves environmentally pleasant by incorporating photo voltaic panels and warmth pumps. The firm has reportedly already acquired over $16 million value of pre-orders and has a waitlist three months lengthy. Its lowest-priced providing is a 120-square-foot studio that prices $26,900, whereas its costliest and largest residence is a 900-square-foot two-bed that goes for $204,900 (these costs don’t embody the land, basis, supply, or utility hookup prices).
Azure’s planning to begin delivering studios by the tip of this 12 months, and can transfer on to accent dwelling items and houses in 2023. Maguire has nothing however optimism about the way forward for 3D printing in building. “3D printing is a more efficient way of building and it should only get better as we develop the processes, technology, and materials further,” he stated. “I can only see it becoming more and more prominent in [construction] as we move forward.”
Image Credit: Azure Printed Homes